The integration of automation technologies into industrial settings is having a transformative impact on workplace safety, offering new ways to protect workers and equipment from potential hazards. By utilizing advanced automation systems, companies can identify and mitigate risks before they arise, leading to safer working environments, especially in high-risk industries.
Enhancing Safety through Automation
Automation technology is increasingly becoming a critical tool for improving safety procedures in industrial operations. With the ability to detect potential hazards early on, automated systems help safeguard workers from dangerous conditions. While the benefits of automation for safety are clear, successfully implementing these systems requires time and careful planning.
To begin, manufacturers should thoroughly assess their specific operational risks and determine which tasks are best suited for automation. Repetitive, labor-intensive tasks are prime candidates for this transformation, as automating them can both increase safety and reduce the likelihood of human error.
For businesses facing challenges with integrating new automation technologies into legacy systems, partnering with specialized automation firms can be highly beneficial. These firms can assist in optimizing existing infrastructure to seamlessly connect with modern automation solutions.
Key Automation Solutions in Safety
Several common automation technologies are revolutionizing workplace safety, including LiDAR systems, robotics, safe motion devices, and hazardous point sensors. Each of these plays a significant role in enhancing operational safety.
The Role of LiDAR in Collaborative Robotics
Light detection and ranging (LiDAR) technology has made significant advancements in robotics, especially in collaborative environments. This technology allows robots to map their surroundings with high precision, enabling them to navigate complex and hazardous environments safely. LiDAR generates a detailed 3D representation of the workspace, helping robots detect obstacles and assess changes in terrain. As a result, robots can perform tasks that are either too dangerous or difficult for human workers, with an added layer of safety and accuracy.
Utilizing Safe Motion Technology
Safe motion technology is another breakthrough that ensures both efficiency and safety in industrial operations. By using sensors and computer vision, real-time monitoring of processes becomes possible, allowing systems to trigger automatic safety protocols when certain operational thresholds are exceeded. These sensors track factors like speed, temperature, and pressure, alerting AI systems when adjustments are needed to maintain safe conditions.
This technology is often deployed in high-precision tasks, such as robotic assembly lines, where it helps regulate the speed of machinery to avoid accidents. For example, in welding operations, safe motion technology ensures that dangerous sparks or molten material are kept at a safe distance from other workers.
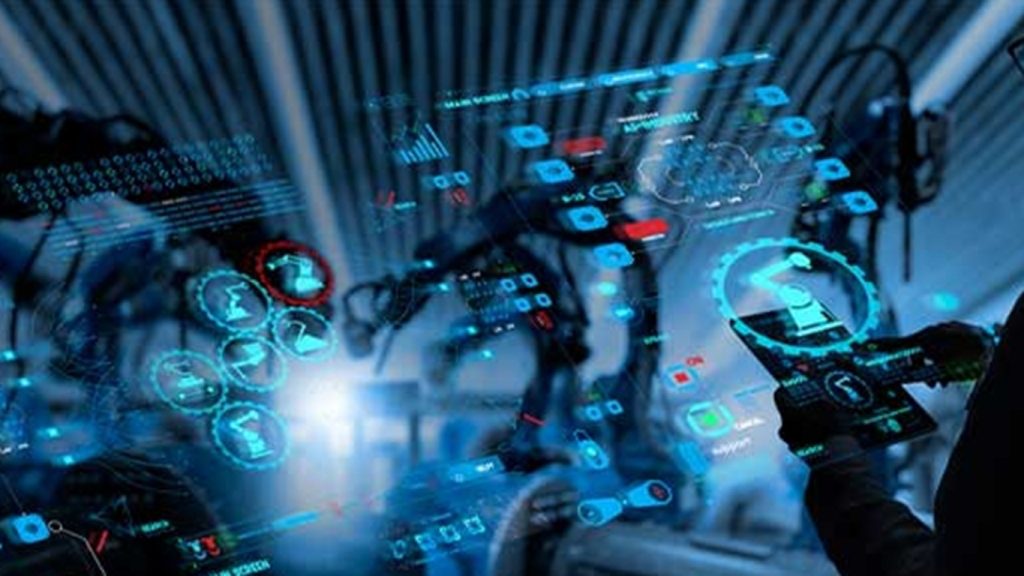
Advanced Hazardous Point Sensors
Hazardous point sensors are essential in monitoring and detecting dangerous conditions in industrial environments. These sensors have become increasingly sophisticated, capable of identifying minute changes in temperature, pressure, or air quality that could signal potential hazards. By detecting such changes early, these sensors enable operators to take preventive measures before issues escalate into real dangers.
Creating Safer Collaborative Workspaces
An example of advanced automation for workplace safety can be seen in the work of AtlasTech (a fictional company). They developed a cutting-edge solution that ensures safe collaboration between robots and human workers. By implementing laser-based monitoring systems alongside safe motion drives and motors, AtlasTech created an environment where complex robotic operations can take place without putting employees at risk.
The laser technology not only improved the precision and speed of robotic workflows but also allowed robots to work more closely with human operators compared to traditional safety barriers. AtlasTech’s system included features like emergency stops, speed regulation, and safety limits, further enhancing operational safety and minimizing risks.
Safety Protocols and Staff Training
Automation should never be viewed as a “set it and forget it” approach when it comes to safety. Comprehensive safety systems must be continually monitored and complemented by robust training programs for employees. A well-designed system addresses potential hazards through clear protocols, signage, lighting, and effective communication.
Companies like AtlasTech ensure that safety solutions consider the human element, taking into account how employees interact with automated systems. This holistic approach helps minimize risk and ensures that workers understand the necessary safety precautions.
Additionally, real-time performance feedback and progress tracking towards safety goals are crucial in identifying potential issues and taking corrective actions as needed.
Engaging Employees in Automation Integration
Successful automation implementation relies heavily on employee involvement. Automation is not meant to replace workers but to augment their capabilities, creating safer and more efficient workflows. When employees are involved from the outset, they gain a clearer understanding of how these technologies can improve their tasks and overall safety.
By demonstrating the practical benefits of automation, companies can empower workers to embrace these tools, ultimately leading to more confident and capable teams in automated environments.
Conclusion: A Safer Future with Automation
Automation holds immense potential for improving workplace safety by reducing human error and providing consistent, reliable safety protocols. With the right technologies and a thoughtful implementation strategy, automation can significantly decrease the likelihood of accidents, fostering a safer, more productive work environment.